Laminate materials have become an integral part of various industries due to their excellent properties such as durability, resistance to wear and tear, and aesthetic appeal.
These materials are widely used in furniture, flooring, and construction industries.
However, to ensure the quality and reliability of these materials, it is essential to adhere to specific quality assurance and testing standards.
This article will discuss the importance of quality assurance and testing standards for laminate materials and the steps involved in the process.
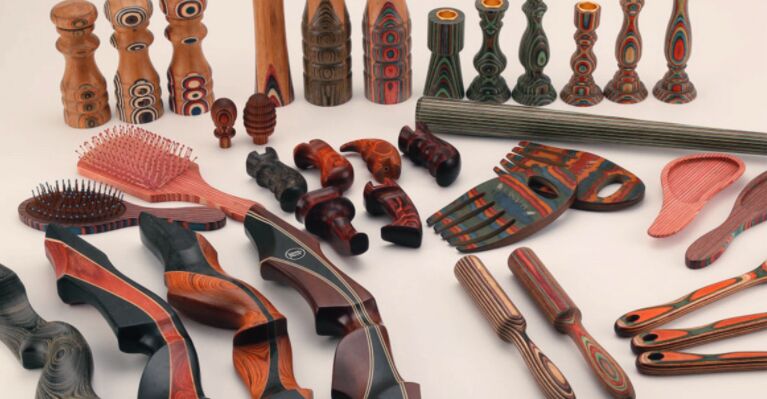
Importance of Quality Assurance and Testing Standards
Quality assurance and testing standards play a vital role in ensuring that laminate materials meet the required specifications and perform optimally in their intended applications.
These standards help manufacturers identify potential defects or issues in the material during the production process, thereby ensuring the production of high-quality products.
Moreover, adherence to these standards helps in maintaining consistency in the quality of laminate materials, which is crucial for customer satisfaction and brand reputation.
Testing Standards for Laminate Materials
There are several testing standards that have been established for laminate materials, including but not limited to:
1. Abrasion Resistance: This test measures the material’s ability to withstand wear and tear caused by friction or rubbing. The results of this test help determine the durability and longevity of the laminate material in various applications.

2. Impact Resistance: This test evaluates the material’s ability to withstand sudden impacts without breaking or cracking. It is particularly important for flooring and furniture applications, where the material may be subjected to heavy loads or dropped objects.
3. Scratch Resistance: This test assesses the material’s resistance to surface damage caused by sharp objects or abrasives. High scratch resistance ensures that the laminate material maintains its appearance and functionality over time.
4. Water Resistance: This test measures the material’s ability to resist damage or warping when exposed to water. It is crucial for applications such as kitchen countertops and bathroom vanities, where the material may come into contact with moisture.
5. Adhesion: This test assesses the bond strength between the different layers of the laminate material. A strong adhesion ensures that the material remains intact and does not delaminate during use.
Quality Assurance Process for Laminate Materials
The quality assurance process for laminate materials involves several steps to ensure that the final product meets the required standards. These steps include:
1. Raw Material Inspection: The quality assurance process begins with the inspection of the raw materials used in the production of laminate materials. This includes checking the physical and chemical properties of the materials to ensure they meet the specified requirements.
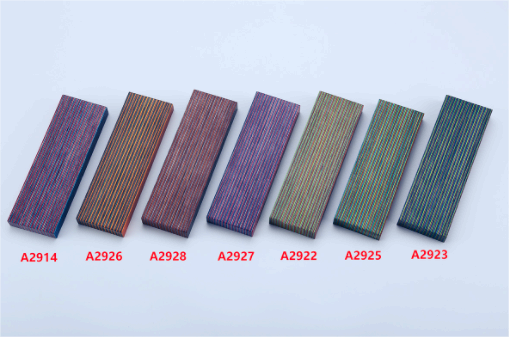
2. Production Monitoring: During the production process, regular monitoring is essential to ensure that the manufacturing process is within the specified parameters. This includes monitoring the temperature, pressure, and speed during the lamination process.
3. Sampling and Testing: Samples of the laminate material are taken at regular intervals during the production process for testing. These samples are tested for various properties, such as abrasion resistance, impact resistance, and water resistance, to ensure they meet the required standards.
4. Statistical Process Control: Statistical process control techniques are used to monitor the production process and identify any variations or trends that may affect the quality of the laminate material. This helps in taking corrective actions in a timely manner.
5. Final Inspection: Once the production process is complete, a final inspection is conducted to ensure that the laminate material meets all the specified quality standards. This includes checking the dimensional accuracy, surface finish, and overall appearance of the material.
6. Certification: After successful completion of the quality assurance process, the laminate material is certified as meeting the required standards. This certification provides assurance to the customers about the quality and reliability of the material.
Conclusion
Quality assurance and testing standards are essential for ensuring the production of high-quality laminate materials. This is particularly true for us, a professional manufacturer of high-quality colored laminated woodsince 2005. With a factory covering an area of 16,000 square meters, we have established a strong supply capacity and mature industrial chain in China.
As a company that integrates technology development, application promotion, production, and sales, we warmly welcome both OEM and ODM projects. Our use of Baltic birch as raw material ensures the production of colored laminated wood that is not only strong and stable but also features bold and personalized colors that can stimulate your imagination and creativity.
We take quality assurance and testing standards very seriously. Our colored laminated wood is FSC and ISO 9001 certified, guaranteeing the highest quality and reliability. From raw material inspection to production monitoring, sampling and testing, statistical process control, final inspection, and certification, we adhere to the strictest quality standards at every step.
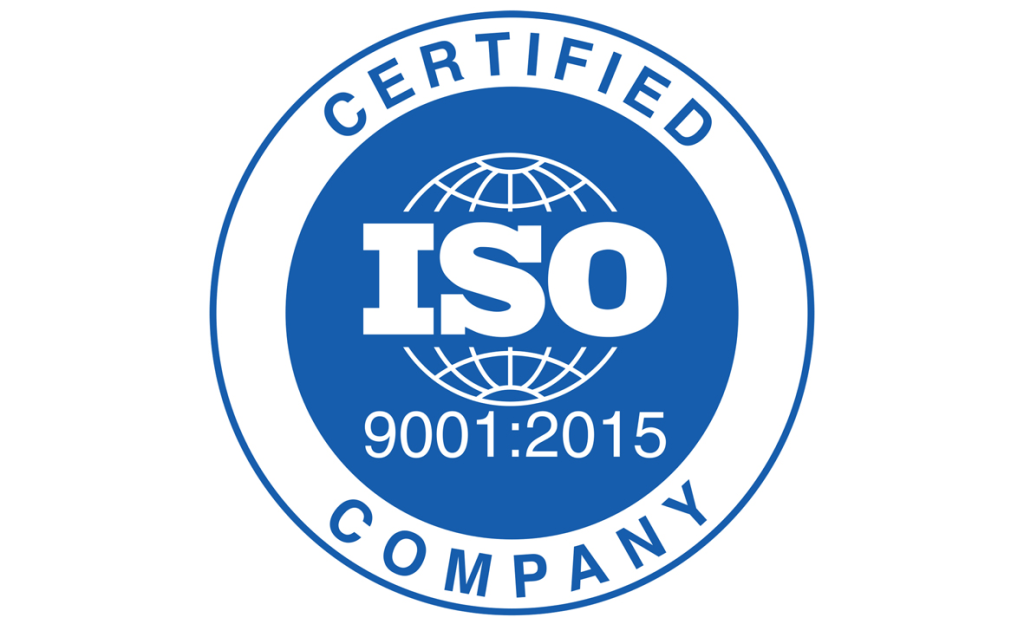
Whether you need standard or special, demanding wood products, our colored laminated wood is an excellent choice. We are committed to providing our customers with high-quality, reliable products that meet their needs and exceed their expectations. Choose us, and you will not be disappointed.